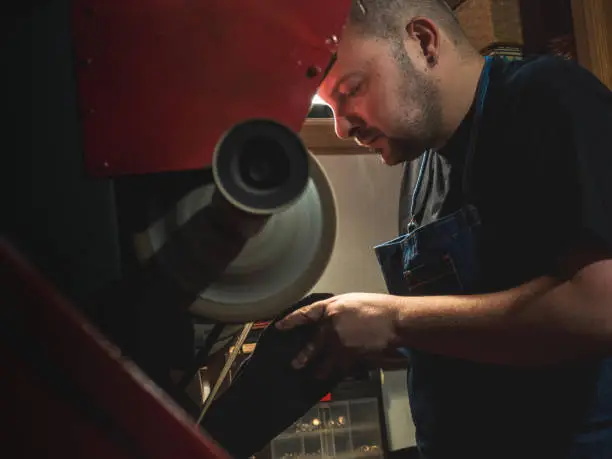
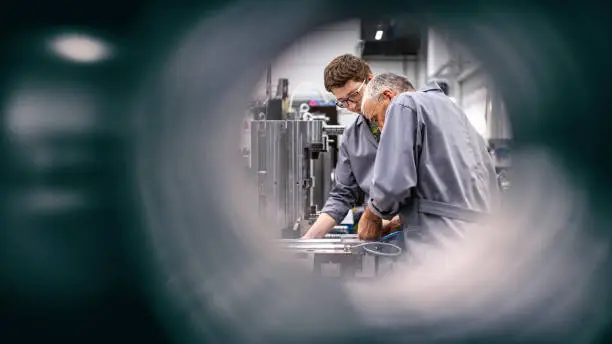
Quality Control and Assurance in Metal Spinning
In precision engineering, tolerances are measured in microns, making quality control paramount. Metal spinning, a specialised form of metalworking, is no exception. At Tanfield Metal Spinners, maintaining the highest standards of quality is not just a practice but a philosophy embedded within every stage of the production process.
This blog explores the stringent quality control and assurance methods that keep Tanfield Metal Spinners at the forefront of the industry and trusted by clients across sectors ranging from agriculture to the food industry.
What Is Metal Spinning?
Metal spinning, also known as spin forming, is a method of shaping flat sheets or tubes of metal into complex shapes. It’s a highly versatile process that creates everything from domes and cylinders to more complex forms such as hollow, circular shapes. The process involves spinning a metal disc or tube at high speed while shaping it against a mould using tools or rollers. This results in precisely formed parts, ideal for industries requiring strong, seamless components. However, achieving this level of precision demands rigorous quality control.
The Importance of Quality Control in Metal Spinning
In metal spinning, even minor defects can lead to significant issues in the final product, affecting functionality, safety, and longevity. For example, a slight variation in wall thickness or an unnoticed material flaw could cause a component to fail, potentially leading to costly downtime or, worse, catastrophic equipment failure. At Tanfield Metal Spinners, quality control is an integral part of every stage of production, from material selection to final inspection.
As one of the leading metal spinners in the UK, Tanfield’s adherence to ISO 9001 standards ensures consistency and excellence. ISO 9001 is the international benchmark for quality management systems, requiring organisations to meet rigorous standards for every aspect of their operations. But at Tanfield, ISO 9001 is more than just a certification—it’s a tool for continual improvement.
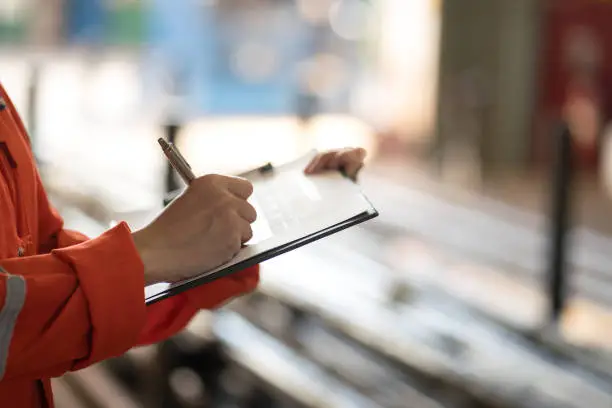
ISO 9001: A Foundation for Quality Assurance
Tanfield Metal Spinners’ ISO 9001 certification provides a framework that ensures every product they deliver meets the exacting standards their clients and the industry expect. The ISO 9001 standard has improved decision-making processes and fostered a culture of continuous improvement across the business.
Tanfield’s quality control team conducts routine inspections at every stage of the metal spinning process, including initial raw material inspections, in-process checks, and final product testing. These checks help ensure that each part meets customer specifications and conforms to industry regulations.
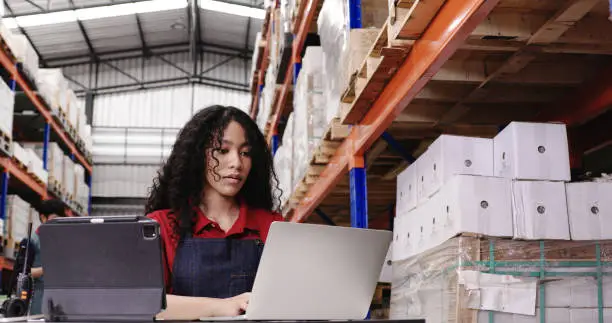
Quality Control Methods at Tanfield Metal Spinners
At Tanfield, quality control is applied at every stage of production, using a combination of advanced technology and time-tested techniques. The following are some of the standard inspection points used in their process:
1. ID/OD Measurements: The internal and external diameters of the spun metal are carefully measured to ensure the product will fit precisely into its intended application. Variations in these measurements can cause significant issues in assembly or operation.
2. Overall Height and Radius: The height and radius are checked to confirm the correct dimensions. Any deviations can result in the product not fitting or functioning as required.
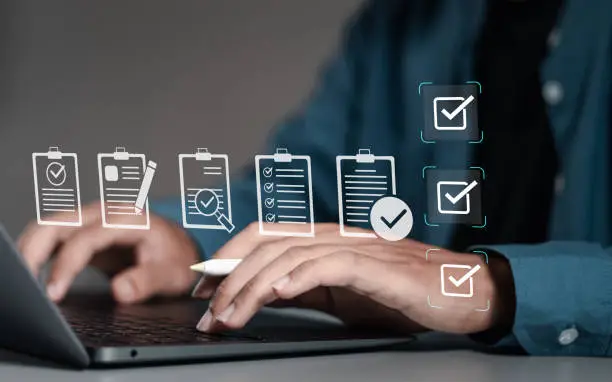
3. Material Thickness: One of the critical aspects of metal spinning is controlling the thickness of the material during the spinning process. Post-spinning inspections ensure the final part has the correct minimum material thickness, avoiding weak spots that could cause premature failure.
4. Spherical and Flatness Checks: Depending on the component’s intended use, the flatness of the spun metal surface and the uniformity of any spherical features are also examined to guarantee compliance with design specifications.
5. Pass/Fail Gauges: Pass/fail gauges are often used to expedite inspections without compromising accuracy. These allow Tanfield’s technicians to quickly determine whether a component meets customer demands, speeding up the production process while ensuring consistency.
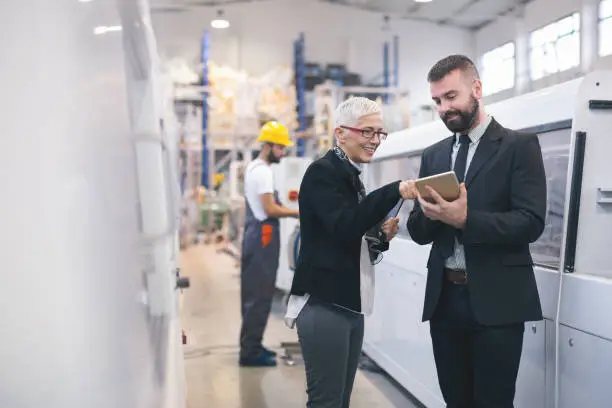
In addition to these standard checks, Tanfield offers a range of additional inspection services. These include First Article Inspection Reports (FAIR) and the Production Part Approval Process (PPAP), which are essential for industries with strict regulatory requirements, such as the aerospace or automotive sectors.
How Quality Control Drives Innovation
One of the key benefits of Tanfield’s commitment to ISO 9001 and stringent quality control is that it frees up resources to focus on innovation. By ensuring that their core processes run smoothly and efficiently, Tanfield can devote more time and effort to research and development. This facet is crucial in an industry like metal spinning, where advances in materials and manufacturing techniques are continually driving new possibilities.
For example, Tanfield always seeks ways to reduce lead times without sacrificing quality. Their ability to deliver complex, high-precision spun metal components on tight schedules makes them a preferred partner for industries ranging from renewable energy to food processing.
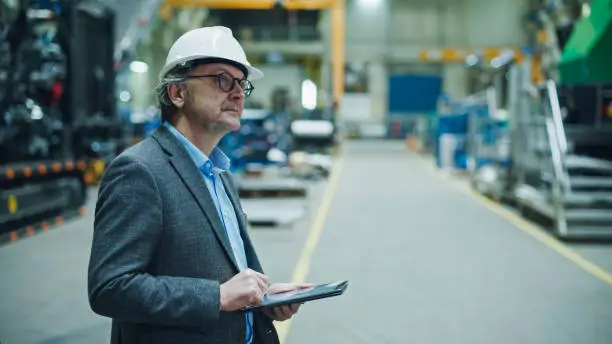
Why Choose Tanfield Metal Spinners?
With a history dating back to 1984, Tanfield Metal Spinners has built a reputation for excellence and prides itself on its flexibility and commitment to meeting its clients’ needs. Whether the customer requires a prototype or a large production run, Tanfield can tailor its services to suit them. They offer bespoke metal spinning solutions, from small, intricate parts to large-scale production, making them one of the UK’s most adaptable metal pressing companies.
Their 35,000 sq-ft facility, equipped with fully automated spinning lathes, allows Tanfield to meet the most demanding production schedules without compromising on quality. Whether working with thin sheets of aluminium or thick stainless steel, they maintain the highest level of precision throughout every project.
Their focus on quality control at every stage of production and adherence to ISO 9001 standards make them a trusted partner for businesses across the UK and beyond. If you’re looking for reliable metal spinners, Tanfield Metal Spinners should be your first call.